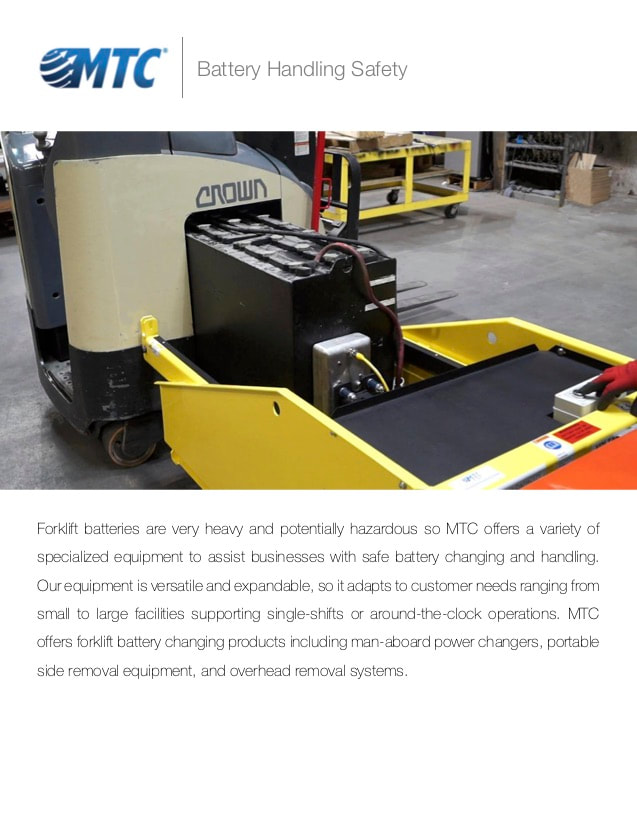
Battery Handling Safety Guide
Get a copy of the battery handling safety information on this page as a single PDF document that makes saving, printing, and sharing this information very convenient.
download as a pdf fileGet a copy of the battery handling safety information on this page as a single PDF document that makes saving, printing, and sharing this information very convenient.
download as a pdf fileIt is important to perform forklift battery inspections before a forklift is used and before and after the battery is charged. Persons performing battery inspections should follow all of the requirements and recommendations of the forklift’s and battery’s original equipment manufacturer (OEM). Consult with the appropriate manufacturer for instructions if you prefer to use following best practices and determine they do not match their guidelines. WARNING: Persons are required to wear personal protective equipment (PPE) whenever workplace hazards exist including those related to forklifts and their batteries. Consult OSHA and other applicable regulations to determine and conform to PPE requirements before performing forklift battery inspections. Best practices for forklift battery inspection include but are not limited to the following:
The charging of forklift batteries should only be performed by trained staff to minimize avoidable personal injury risk and damage to forklift, battery, and charging equipment. It is important for the person charging a battery to begin with an appropriate inspection of the battery and charger, following all of the requirements and recommendations of the battery’s and charger’s original equipment manufacturer (OEM).
WARNING: Persons are required to wear personal protective equipment (PPE) whenever workplace hazards exist including those related to forklifts and their batteries. Consult OSHA and other applicable regulations to determine and conform to PPE requirements before performing forklift battery inspections.
Best practices for forklift battery charging safety include but are not limited to the following:
Maintenance of lead-acid batteries involves exposure to dangerous levels of electricity, potential exposure to hazardous materials, and the movement of heavy items and equipment so it should be performed by trained technicians only. The processes involved during maintenance may vary for different forklifts, battery types and manufacturers, and servicing equipment. Therefore, a trained technician is the best person to determine the correct maintenance requirements for each situation.
WARNING: Persons are required to wear personal protective equipment (PPE) whenever workplace hazards exist including those related to forklifts and their batteries. Consult OSHA and other applicable regulations to determine and conform to PPE requirements before performing forklift battery inspections.
Best practices for forklift battery periodic maintenance include but are not limited to the following: